Medium Density Fiberboard (MDF) is a composite wood product made from the amalgamation of wood fibers obtained from hardwood or softwood residuals. These fibers are combined with a resin binder and wax, and then subjected to high pressure and temperature to form dense panels. MDF is renowned for its uniform density, smooth surface, and consistent strength, making it an ideal material for a wide range of applications in woodworking and furniture manufacturing.
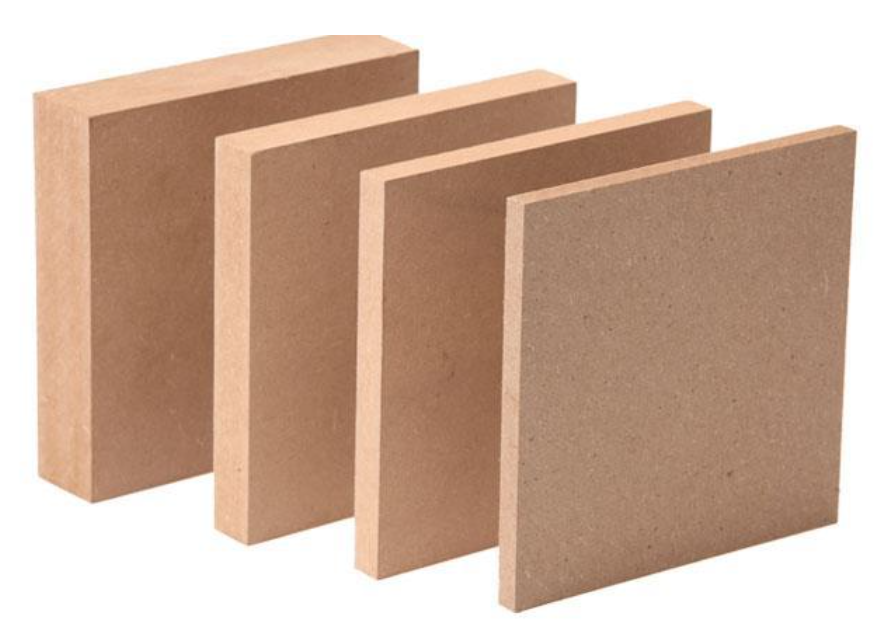
Properties Of MDF
1. Density: As the name suggests, MDF has a medium density, typically ranging from 600 kg/m³ to 800 kg/m³ (37 lb/ft³ to 50 lb/ft³). This density range offers a balance between strength and workability, making MDF suitable for both structural and decorative purposes.
2. Uniformity: MDF is renowned for its uniform density and composition throughout the panel. Unlike natural wood, which may contain knots, voids, or other irregularities, MDF panels have a consistent texture and appearance, making them ideal for applications requiring smooth surfaces.
3. Smooth Surface: MDF panels have a smooth and flat surface that is free from grain patterns or imperfections commonly found in natural wood. This smoothness allows for easy painting, staining, or laminating, resulting in a flawless finish for furniture, cabinetry, and interior fittings.
4. Machinability: MDF is highly machinable, meaning it can be easily cut, drilled, routed, and shaped using standard woodworking tools. Its uniform density and lack of grain direction facilitate precise machining, allowing for intricate designs and customizations.
5. Dimensional Stability: MDF exhibits excellent dimensional stability, meaning it is less prone to expansion, contraction, or warping compared to natural wood. This stability makes MDF panels suitable for applications requiring tight tolerances and consistent dimensions.
6. Strength and Durability: Despite its relatively low density, MDF offers good strength and durability for many applications. MDF is known for its uniform density throughout the panel, which contributes to its stability and machining properties. The resin binder and uniform distribution of wood fibers contribute to its structural integrity, enabling MDF panels to withstand loads and impacts encountered in everyday use.
7. Moisture Resistance (Variants): The primary difference between moisture-resistant MDF and standard MDF lies in the resin formulation used during manufacturing. Moisture-resistant MDF typically incorporates moisture-resistant or water-repellent additives into the resin binder, enhancing its ability to withstand moisture penetration. Common additives may include wax emulsions, phenolic resins, or melamine formaldehyde resins, which provide hydrophobic properties to the panel. Moisture-resistant MDF is particularly well-suited for applications where exposure to moisture or high humidity is a concern.
8. Fire Resistance (Variants): Fire-resistant MDF incorporates fire-retardant additives into the resin binder during the manufacturing process. Common additives include fire-retardant chemicals such as ammonium polyphosphate, aluminum hydroxide, or magnesium hydroxide, which act to suppress combustion and slow down the spread of flames. The formulation of FR-MDF is carefully designed to meet specific fire safety standards and regulations.
Manufacturing Process of MDF Boards
1. Raw Material Preparation:
The first step in material preparation involves converting raw wood into fibers. This is typically done using mechanical processes such as refining or grinding.
Wood logs are debarked to remove the outer bark layer, then chipped into small pieces using chippers or slicers.
Hammer Milling:
Wood chips are fed into a hammer mill, where they are repeatedly struck by rotating hammers until they are reduced to fibrous particles.
Refining:
Wood chips are refined in a disc refiner, where they pass between rotating discs with sharp edges, resulting in the separation of fibers.
Steam Explosion: In some advanced processes, steam explosion techniques are employed to soften the wood chips, making them easier to refine into fibers.
2. Blending and Drying:
Additionally, waxes may be added to improve water resistance and reduce internal friction during the manufacturing process.
The blended mixture is then dried to reduce moisture content to the desired level, typically around 5-8%.
3. Forming the Mat:
The thickness of the mat can be adjusted based on the desired final thickness of the MDF panel.
4. Hot Pressing:
This combination of heat and pressure activates the resin binder, causing it to cure and bond the wood fibers together.
The duration of pressing can vary depending on the thickness and density requirements of the MDF panel, typically ranging from a few minutes to half an hour.
5. Cooling and Trimming:
Once cooled, the edges of the panel are trimmed to achieve the desired dimensions and ensure uniformity.
6. Finishing:
Depending on the intended application, the MDF panels may be coated with paints, laminates, or veneers to enhance aesthetics and durability.