The salt spray test, also known as salt fog testing or salt corrosion testing, is a standardized method used to evaluate the corrosion resistance of metal coatings. It’s a crucial process in various industries where protection against corrosion is essential, such as automotive, aerospace, marine, and metal furniture manufacturing.
Salt spray tests typically last between 24 and 1,000 hours, or more for some coatings. The test involves exposing a material to a salt mist at a temperature of about 37°C, causing the material to corrode more quickly than in a normal environment. The samples are constantly wet, and performance is rated by recording the number of hours it takes to reach defined levels of surface rusting. There are four types of salt spray tests i.e. Neutral salt spray test (NSS), Acetate mist test (AASS), Copper accelerated acetate mist test (CASS), and Alternating salt spray test.
Sample Preparation
The first step involves preparing the test samples. These samples typically consist of metal substrates coated with various types of protective coatings like zinc, chrome, nickel, or paint.
Samples are often cleaned thoroughly to remove any contaminants that could affect the test results. This ensures that the coating’s performance is accurately assessed.
Test chamber setup
A specialized salt spray chamber, also known as a salt fog chamber, is used for conducting the test. This chamber provides a controlled environment where the saltwater solution is atomized and sprayed onto the test samples.
The chamber is equipped with temperature and humidity controls to maintain consistent testing conditions throughout the experiment.
Preparation of salt solution
A salt solution is prepared by dissolving sodium chloride (NaCl) in water. The concentration of the salt solution can vary depending on the specific test standard being followed. Typically, concentrations range from 5% to 10% NaCl by weight.
Some standards may require the addition of other chemicals to simulate specific environmental conditions accurately.
Loading samples into the chambers
The prepared test samples are placed inside the salt spray chamber. Care is taken to ensure that the samples are positioned in a way that they are evenly exposed to the salt spray.
Samples may be mounted vertically or horizontally, depending on the requirements of the test standard.
Exposure to salt spray
Once the samples are loaded into the chamber, the salt spray test begins. The chamber is operated according to the specified test parameters, including temperature, humidity, and duration of exposure.
Samples are subjected to a continuous spray of saltwater solution, simulating the corrosive effects of salt-laden environments such as coastal regions or industrial settings.The duration of exposure can vary depending on the test requirements and the expected service life of the coating being evaluated. Common test durations range from a few hours to several hundred hours.
Monitoring and inspection
Throughout the test, samples are periodically inspected to assess the extent of corrosion. Visual inspections are conducted to observe any changes in the appearance of the coatings, such as blistering, rusting, or peeling.
Measurements of coating thickness may be taken before, during, and after the test to quantify the extent of corrosion damage. Any signs of corrosion or degradation are carefully documented for further analysis.
Evaluation and analysis
After the specified test duration has elapsed, the samples are evaluated for corrosion damage. This evaluation may involve comparing the condition of the coated samples before and after exposure to the salt spray.
Various analytical techniques, such as microscopy, spectroscopy, or electrochemical testing, may be employed to assess the corrosion mechanisms and identify any weaknesses in the coating.
Data collected during the test is analyzed to determine the coating’s performance, including its resistance to corrosion, adhesion to the substrate, and overall durability.
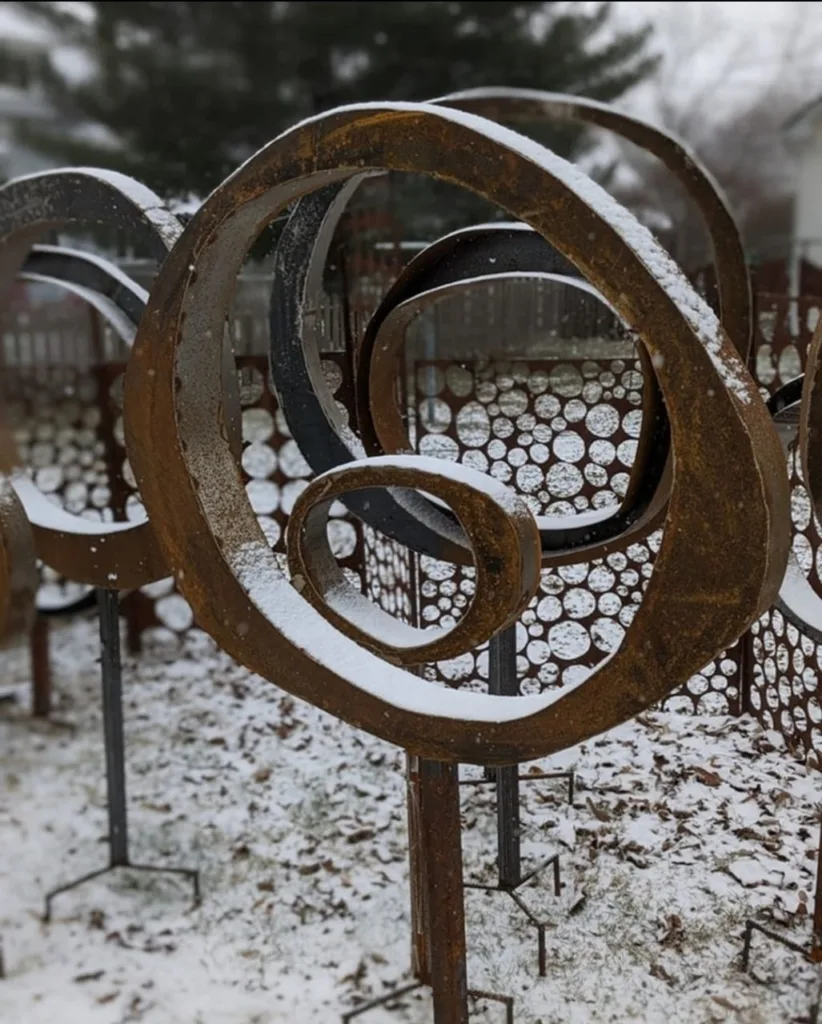
Interpretation and application
The findings of the salt spray test are used to assess the suitability of the coating for its intended application. Manufacturers can use this information to optimize coating formulations, improve manufacturing processes, or select alternative materials with better corrosion resistance.
Regulatory agencies may also use salt spray test results to verify compliance with industry standards and regulations governing corrosion protection in specific applications.